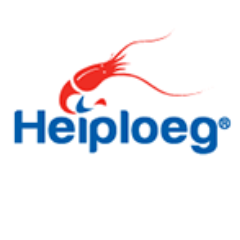
How do you develop a future-proof secondary packing concept?
Heiploeg
CEO
Pancake manufacturer Cérélia in Sliedrecht has implemented three automation projects in the past year. Important partner in this is BluePrint Automation. In addition to installing a number of case packers and delta robots, the Woerden-based machine manufacturer also provided the complex programming and mechanical solution for the bag feeding systems.
Every day, millions of pancakes and pancake-bites come out of the factories of the international food producer Cérélia. Production is spread over 12 production plants worldwide. One of those plants is in Sliedrecht and stems from the acquisition of De Bioderij in 2015. Here, the company produces pancakes, among other things, for the well-known Jan brand and for various private labels. The cooperation with BluePrint Automation (BPA) dates back to the early days. At the Macropack in 2000, Bioderij founder Jan Vink made the first contacts. Hans Verhoeff, BPA sales manager, still remembers it well. 'In those early days, the first production line was set up with a BPA Gantry robot. Since then we have supplied several case packers and robots worldwide for packing bags and trays into boxes and for packing naked product.'
Pancake-bites lines
In 2022, Cérélia decided to further optimize its pancake-bites lines and expand from three to four case packers. The optimization was necessary in part because Cérélia was switching from deep-draw packaging to block bottom bags. This resulted in significant savings in plastic packaging material. The fourth case packer was needed to pack bags of pancake-bites in SRP boxes not only lying down but also standing up. Standing packing was done manually. For this automation, BPA supplied the Spider 300v, which uses a special cassette to collect the pouches, tilt them and place them upright in the box. This Spider 300v can be quickly converted from lying to standing packing. 'Straight packing in SRP boxes used to be done by hand,' says Leendert-Jan van der Hout, project engineer for Cérélia. 'By automating the process, we have saved two workers per shift.'
Programming
Delivery and installation of the new case packer was relatively simple. However, converting the supply to the three other case packer lines, however, required a lot of engineering work. For this, too, BPA was called in. The machine builder provided programming for the infeed belts from the packing machines to the four case packers. These are complex situations in which the various supply flows from bagmakers must be distributed to the four case packers. That requires good synchronization with the machines in the line. 'You want the product to arrive as well as possible at the case packer,' explains Van der Hout. 'For example, no bags may lie on top of each other, because then the vision system rejects them and a reject follows. The better the product supply runs, the fewer corrections there are. That requires specific programming. We left that to BPA, because we can read and write with BPA's programmers.'
Pancake-line
In addition to the pancake-bites line, the pancake-packing line has also been automated. Two BPA delta robots have recently been collecting pancakes with special 3D-printed vacuum heads and placing them in top-seal trays. Here the BPA robots achieve a capacity of thousands of pancakes per hour. 'Previously, this was done by hand,' explains project engineer Michael Driessen. 'Where there used to be six packers on the line packing thousands of pancakes per hour, we saved three packers per shift and the line output has increased significantly.'
Buffering toaster cakes
Another installation, that of the toaster cake packing line, was a considerable challenge, says Michael Driessen. The old line consisted of four BPA robots that stacked the toaster cakes in stacks of 3, 4 or 5 after which 3 to 4 packers placed them in deep-drawing trays. 'In three shifts daily we needed 9 to 12 packers', says Driessen. 'This line is now automated with four delta robots. Bringing in the robotic line was a big job, because the entire facade had to be removed, we had to move the Multivac machine and lift the robot over existing lines.'
The challenge at BPA was in developing a new buffer system for the toaster cakes, says Hans Verhoeff. 'The toaster cakes arrive at the robot by the thousands. Buffering them required the necessary programming and a special construction was needed.' The buffer system consists of four carousels with plastic trays on either side of the BPA robot. It can temporarily hold the toaster cakes if there is a foil change from the thermoformer or if there is a minor malfunction, such as a labeling problem. The buffer can then accommodate a production run of up to 3 minutes, so the entire line does not have to be stopped. "This was a nice challenge for our engineers," says Verhoeff.
Data link
Michael Driessen looks back on the three projects with a good feeling. 'The installations went smoothly and the service from BPA is excellent,' he says. 'When I call them, there is immediate action. That is also necessary, because if we have problems and we stand still, it costs us a lot of money. That's why I always ask our machine suppliers if they want to provide a data connection to their service department, so they can watch remotely to solve the problems.' 'Good communication is essential,' Verhoeff confirms. 'That ensures pleasant cooperation and is the basis for a successful project.'