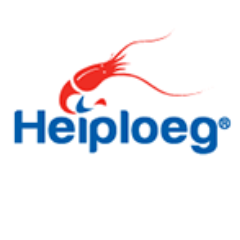
How do you develop a future-proof secondary packing concept?
Heiploeg
CEO
Wrap around cases or trays are designed to pack products into die cut packaging, which forms directly around the product. Traditional RSCs generally have a lot freer space to facilitate the loading of products. The wrap around case offers a tight product, using less material per case as well as giving better strength for palletizing and distribution. The case magazine can hold twice as many wrap around cases versus standard RSC style. On top of that, more flexibility and variation of SRPs (Shelf Ready Packaging) are possible with wrap around cases compared to RSCs.
Secondary packaging is the grouping of several individual items into a secondary container. Depending on your product this may also mean a single product into the container. Secondary packaging solutions are provided after your product has been packaged and is ready to be placed in the shipping container. With so many secondary automated packaging equipment options on the market, how do you know which one to choose?
Your solution will be based strictly on your needs. At BPA, factors such as product and package type, speed, number of recipes and pack patterns and more will be taken into consideration when determining a secondary packaging solution best for you. BPA has a diverse team of experts on hand to assist you through this process.
BPA offers excellent wrap around case packers. The Wraparound 100 is a highly flexible, modern, servo controlled horizontal case packer. It distinguishes itself with its unique Catamaran construction style. This versatile machine is able to produce different case styles, offering you a large size range. Changeovers can be automated by a motor driven system.
Built for a 24/7 production environment where performance and proven technology are of critical importance, the Wraparound 100 answers virtually any wrap around need. It can be expanded with modular infeed systems to handle most products, orientations and speeds. This uses a variety of well proven concepts such as lane dividers, stacking units, stacking belts, racetracks, elevators, aligners, turning stations, tilting units and more.